7 stages that make a quality sock the TABIO quality sock
Tabio’s socks fit completely comfortably as if they were custom made only for you. Our socks are not just ordinary socks, the secrets of the legendary quality and superior comfort are hidden in the details.
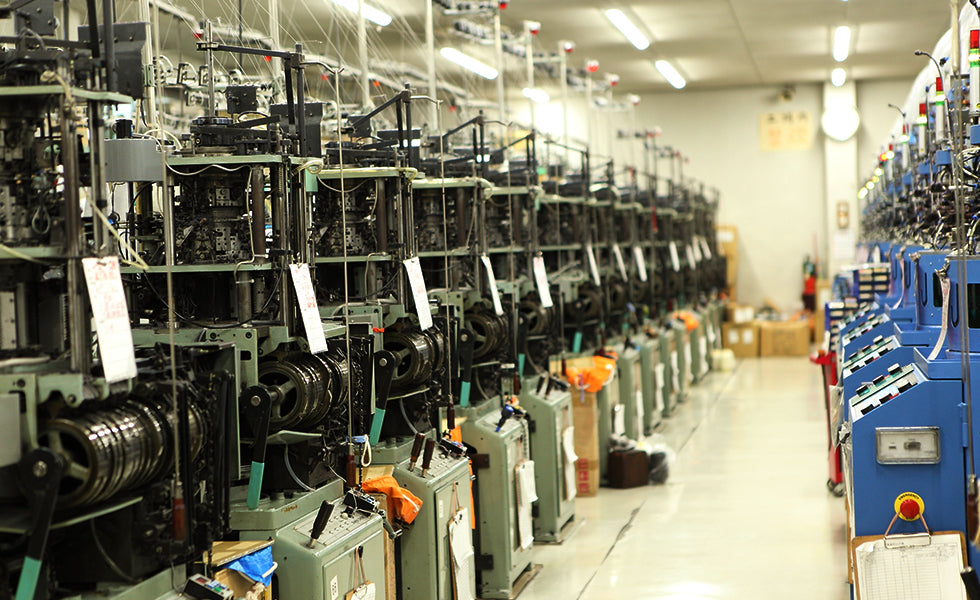
We are using specific kinds of traditional and modern knitting machines
There are various sock knitting machines and we change the knitting machines depending on what kind of socks we want to make. Traditional old type knitting machines are being used to pursue the best texture and comfort for the socks in situations where modern machines cannot guarantee the same texture. Craftsmen carefully adjusts the machines depending on the type of material and a number of other factors, such as the outside temperature and how the humidity affects the way the machine is supposed to be tuned. Some of the machines, like the double cylinder, or Russel machine can only be operated by skilled craftsmen with over 15 years of experience.
One long tubular sock is produced and then divided into individual socks
Aren’t you thinking that socks are knitted one-by-one? Actually, Tabio knits its socks all together in a long tubular shape. In a later step, they are separated and made into the socks that we all know. The latest and most popular machines make socks one by one and are, without a doubt, better for production efficiency. However, Tabio sticks with the old-school, classical machines and still utilizes the tubular production method. Why? The reason is that this way, there is more tension across the fabric as a whole, making the fabric’s face in each sock more beautiful. This is how Tabio prioritizes quality over efficiency and how we spare no effort in producing the perfect pair of socks.
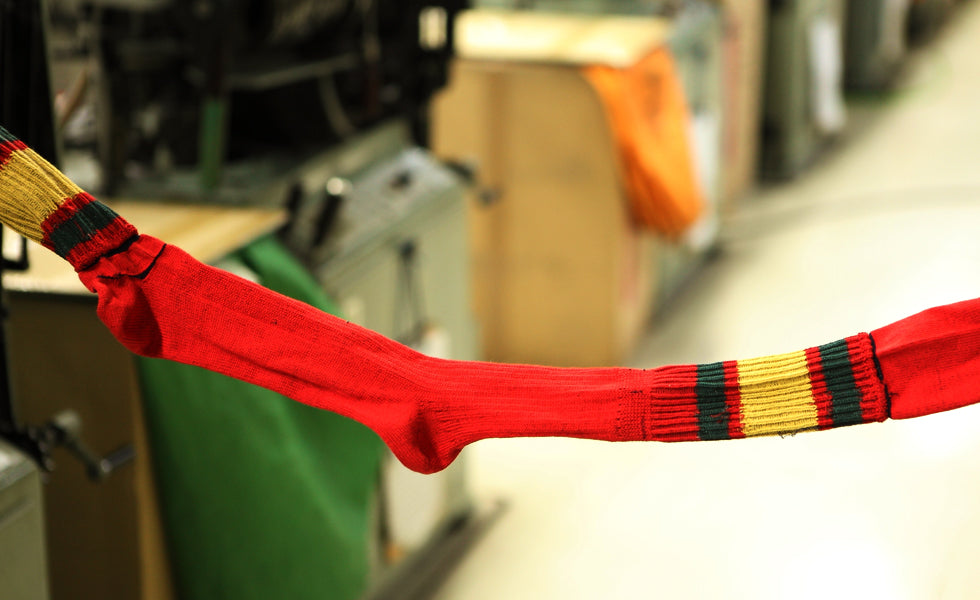
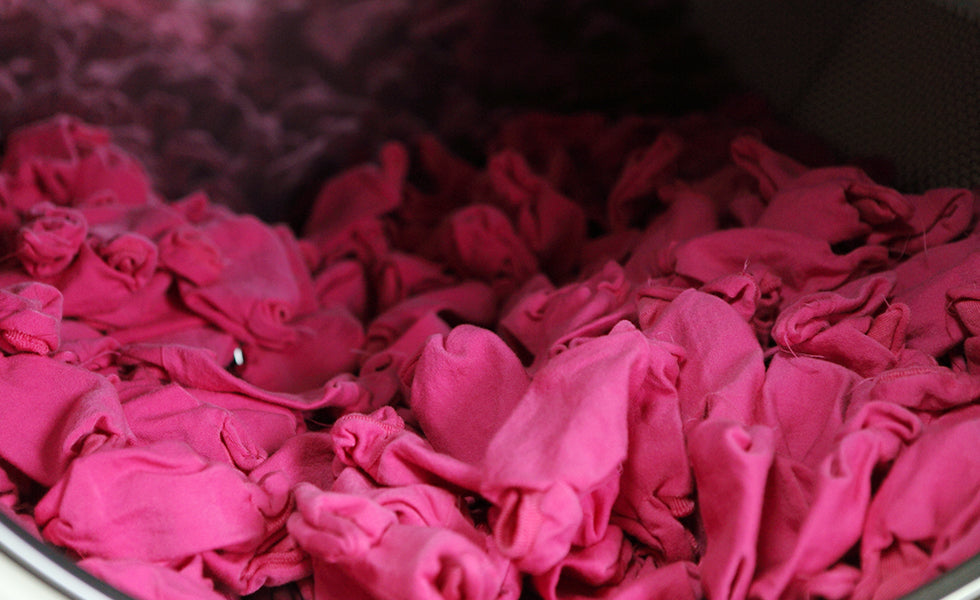
Freshly produced socks are being carefully washed so that they won't shrink
We don’t want you disappointed at your brand new socks shrinking after getting them washed, so we have a method in the factories to minimize the shrinking. We carefully select a specific soap for each type of material to prevent shrinking and achieve the softness of the fabric.
We sew the toe area one by one
In order to create a familiar sock shape for a tubular-shaped sock, we use the ROSSO machine technique and the seamless toe linking craft technique. For the ROSSO technique, we sew the toe area one by one with a sewing machine. Seamless toe linking is an old technique in which the craftsman matches every single stitch that is sewn together. It might sound like an easy task, but it is actually a very intimate and important process.

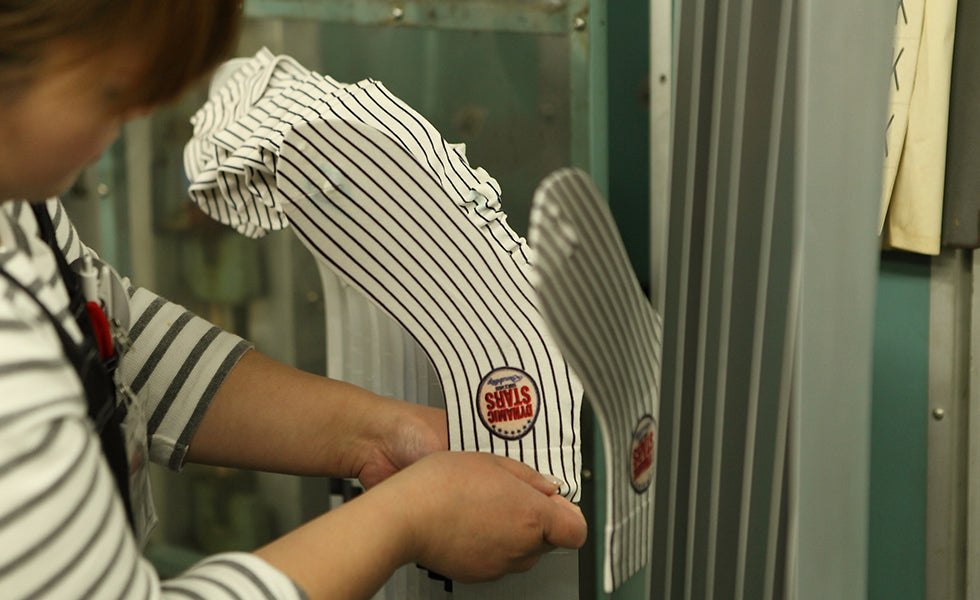
Ironing is another step in creating the legendary Tabio sock
We put Each sock on a feet shaped mold made of aluminum and iron it with a special machine called the “set machine”. This “set machine” can adjust the drying time and steam pressure specifically for each type of sock. That’s why Tabio’s socks look so crisp!
Checking the texture to perfection
Pair large text with an image to tell a story, explain a detail about your product, or describe a new promotion.
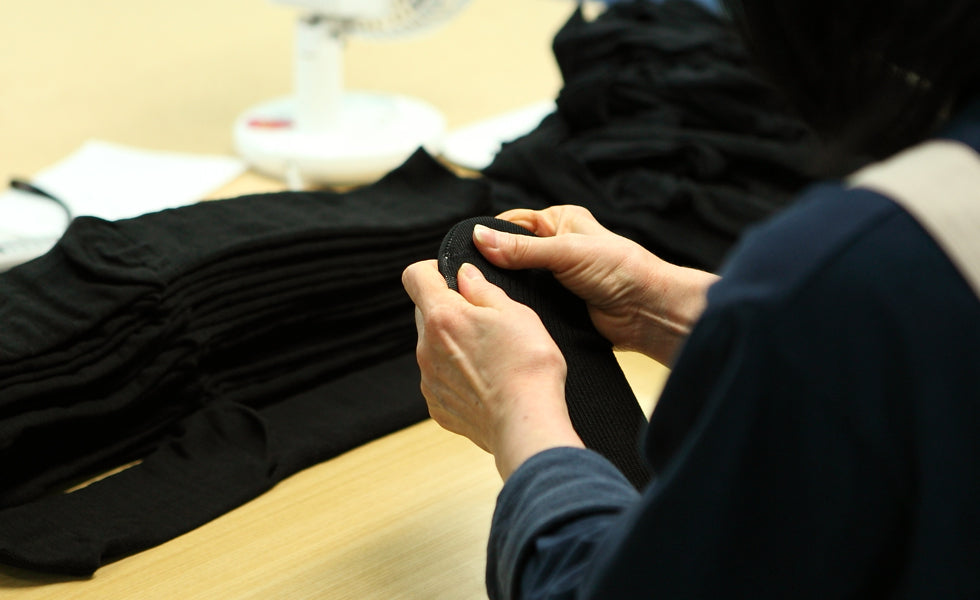
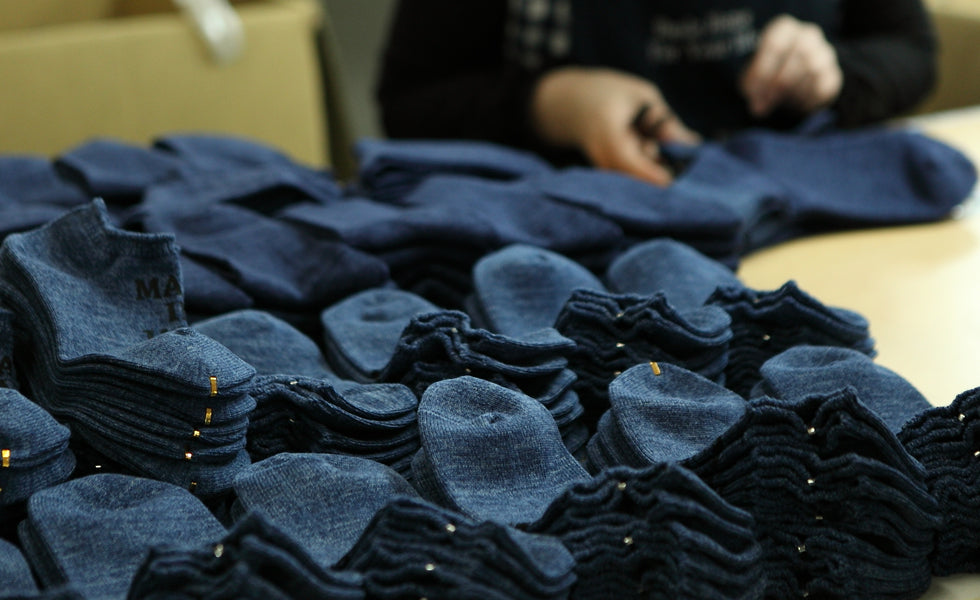
Perfect pairing
Socks need to be a pair. The process of creating pairs is also done by hand. This process is called “pairing”, where we pick one sock that matches another. It’s difficult, especially when dealing with patterned socks. Since each sock has a different pattern, we make pairs more carefully, ensuring there are no pattern differences between the pairs. Each size is paired by hand as well, even 1 mm of a difference is taken seriously when finding the perfect pair.
Tabio has an in-house inspection organization that carefully tests all new Tabio styles. More than 35 items of special equipment are used to ensure new product can represent the legendary Tabio quality. Every issue is detected and fixed before new Tabio style will be approved and slipped on over the Tabio’s customer’s feet. The inspection has extremely high standards. In fact, Tabio has its own quality standards which exceeds the JIS (Japanese Industrial Standards).
Socks are being stretched, skinned, and tested in washing machines with various types of detergents including bleach. Tabio’s quality professionals are doing color resistance control, water absorbency tests, and there is even a running treadmill in the center to do special performance tests for our sports line. This strictly enforced inspection is absolutely necessary to make socks that can withstand harsh environments.